Effluent monitoring – A brewing opportunity
The modern brewery has two operational objectives: maximize production and meet regulator requirements. As any engineer knows, these are not exactly complimentary objectives. So then, what is a brewery to do? It’s simple, monitor.
But, what do we mean by monitor?
The problem
In the traditional wastewater effluent process “monitor” means one thing: composite samplers and lab analysis. In other words, monitoring is a word that is generally associated with expensive, sparse, error prone data. To monitor effectively and economically, the data needs to flow in real-time, without error, and be comparable to lab methods.
Okay, so we need to maximize production, meet regulator requirements, and that this needs to be achieved with real-time data that is both reliable and comparable to lab methods. This implies the need for a monitoring system that can be dropped in place, and that system should also be able to maintain itself, have the smarts to send data to appropriate locations, and alert personnel to events. And, since we are trying to reduce the cost compared to traditional methods, the notion of using consumables or reagents is gone. Much like me at 16 years old looking for a Porsche with the budget of a Lada, our list of options is shrinking dramatically.
We don’t have to settle for the Lada however, since there is one solution – online spectroscopy.
The solution
Traditionally found on a lab bench, spectrometers emit light through a water matrix and measure the absorbance of water at particular wavelengths. Without diving too deep into the science, the constituents of the water matrix uniquely absorb light at particular wavelengths, and thus the amount of each constituent can be measured directly. This means that by simply measuring how light is absorbed by water, we can determine what is in that water. If we take this a step further and measure multiple wavelengths simultaneously, we can construct the “fingerprint” of water, and compensate for cross sensitivities such as turbidity. This allows us to determine key parameters, corresponding to different wavelengths, as seen below.
s::can Messtechnik has spent the better part of 21 years researching, developing, and proving the validity of this method. Further, they have reduced the cost and increased the ruggedness of the spectrometer by packaging it in a probe, known as the spectro::lyser. The spectro::lyser measures absorbance from 190-750nm, discretized into 256 characteristic wavelengths, and leverages “global” calibrations that allow for plug and play measurement of key parameters based on data from water sources around the world.

Real results
We partnered with a well known Vancouver based brewery to solve their dilemma, utilizing the s::can spectro::lyser and pH::lyser pro to monitor their effluent COD, pH and TSS in real-time before it discharges to Metro Vancouver. The data feeds directly into their DCS, ensuring operational awareness, while automated cleaning facilitates low maintenance, stable measurement. A special calibration for the sump pit deployment was created by s::can, allowing for early warning of high loads and, interestingly enough, beer discharge.
Yes, you read that correctly. Beer discharge. Lets talk about that.
The introduction of beer to the water matrix (more specifically yeast) can be pinpointed and consequently monitored in the effluent. While this may seem to be unnecessary, the calibration was proven to be quite necessary when a discharge of 80,000L of beer occurred overnight in a period of 30 minutes. This was both unfortunate (for us beer drinkers), and would not have been caught by the prior 24-hour composite sampler.
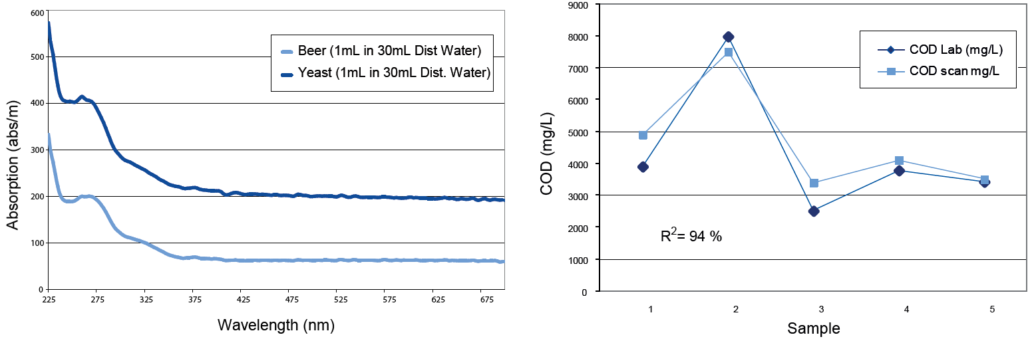
Wrapping it up
Years later, the s::can system has proven itself a valuable process control tool with the brewery. It has provided cost savings by reducing required lab samples, lost product, and it benefits all stakeholders by empowering the brewery to meet permit regulations while maximizing operational efficiency. And they aren’t alone, as breweries throughout the world have begun to take notice and execute on the same process improvements.
Cheers to good beer and the future of making it.
Leave a Reply
Want to join the discussion?Feel free to contribute!